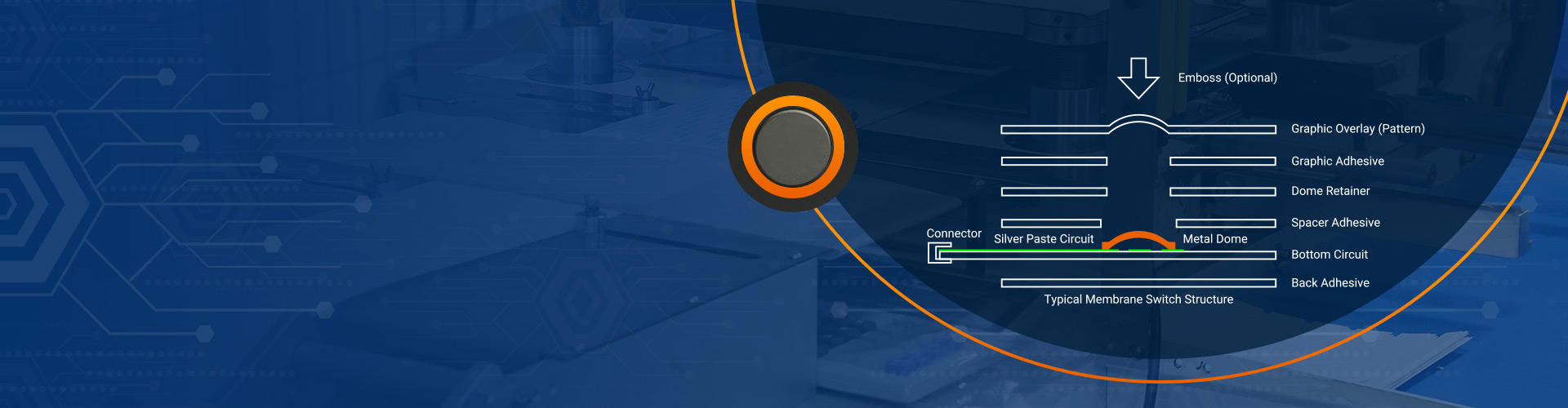
What are membrane switches? Membrane switch design guide
What are membrane switches? Membrane switch design guide
Membrane switches are thin, flexible interfaces that activate a circuit when pressed. Built from multiple flat layers, they offer a clean look, strong durability, and precise control. Commonly used in medical devices, industrial panels, and consumer electronics, they’re known for being reliable, customizable, and space-saving.
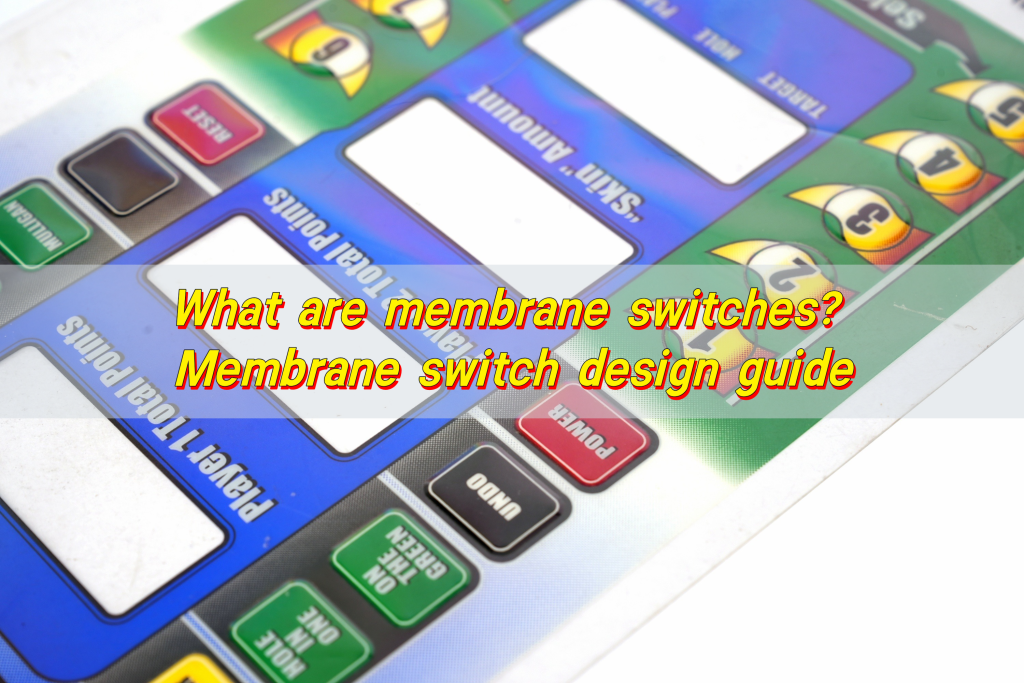
What is membrane switch design?
Membrane switch design is the process of creating a responsive, multi-layered user interface built for touch. It involves engineering multiple flexible layers—each with a specific role—to form a low-profile, high-performance control solution.
Every layer in a membrane switch has a job. The top graphic overlay displays instructions or icons. The spacer layer separates the top from the circuit layer. Pressing a button connects the circuit, sending a signal.
The design process considers factors like actuation force, click response, layout, and overlay clarity. A well-designed switch looks sharp, feels intuitive, and lasts for millions of cycles. It fits the environment, whether that’s a hospital, a factory, or a consumer product. Each decision—from materials to layout—affects the user experience.
Which membrane switch types suit your project?
Each type has its strengths, and picking the wrong one can hurt performance or comfort.
Tactile membrane switches are popular because they offer physical feedback. When pressed, a metal dome or rubber dome collapses and pops back up. They’re ideal for gloves-on applications or noisy areas where visual confirmation is tough.
Non-tactile membrane switches don’t have a click. They provide silent operation and a flat surface. These are common in minimalist designs, medical tools, and household electronics where sleekness matters more than feel.
Backlit switches add visibility in low light. These use LEDs or electroluminescent lighting behind the overlay. They shine through printed icons or text and make nighttime operation easy.
Capacitive switches rely on touch sensing rather than mechanical contact. They allow for ultra-smooth surfaces, often glass-like or plastic. These are perfect for modern, clean designs. Think appliances, elevator panels, or high-end electronics.
Hybrid switches blend types to give the best of both worlds. You might have tactile feedback on frequently used keys, and flat capacitive or non-tactile keys elsewhere.
Choosing the right type means thinking about who’s using the product, where, and how often. If users need a press they can feel, go tactile. If they need silence and sleekness, choose non-tactile.
How to choose materials for membrane switches?
Material choice is a foundation of membrane switch design. It affects not only how the switch feels but also how long it lasts and how well it performs.
The graphic overlay is the outer layer. Polycarbonate and polyester are the main choices. Polycarbonate is easy to print but scratches faster. Polyester is stronger and resists chemicals better. For harsh settings or long-term use, polyester is a smart pick.
Next is the spacer layer, which keeps the circuit layers apart until pressed. It’s often made of adhesive-backed polyester. The thickness needs to match the actuation force and tactile dome size.
The dome layer—only for tactile switches—holds metal or rubber domes. Metal domes offer crisp feedback and long life. Rubber domes are softer and more affordable, but they wear out faster. For industrial or medical use, metal domes are often the better option.
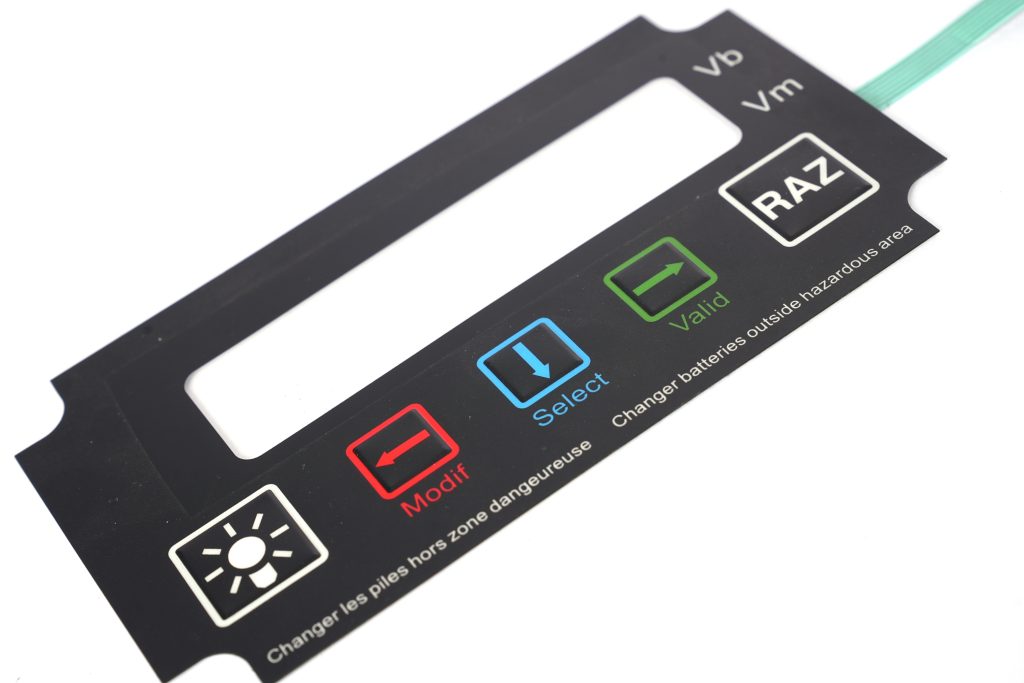
The circuit layer is where the magic happens. This can be a printed silver circuit or a copper flex circuit. Silver ink on PET film is affordable and flexible.
The adhesive layers bond everything together. Reliable adhesives from brands like 3M ensure the layers don’t peel in heat, cold, or humidity. Good material choices lead to longer life, better user experience, and fewer problems later.
How to reduce costs in membrane switch design?
Start with simplified design layouts. Avoid odd shapes or sizes unless necessary. Keep graphics clean. Overly detailed or full-color overlays drive up printing expenses.
Minimize the number of layers. If your application doesn’t need tactile feedback or lighting, skip them. Use bulk ordering when possible. Larger runs spread the setup cost across more units, dropping the per-piece price.
Standardize components. Using standard dome sizes, common adhesives, and available circuit layouts speeds up production and lowers sourcing costs. Custom domes or odd circuit shapes usually cost more and take longer.
Focus on user needs, and avoid adding unnecessary features. The right choices will deliver a quality switch without stretching the budget.
What makes a good membrane switch panel?
A good membrane switch panel feels natural, works flawlessly, and lasts through countless uses. It begins with a clean, intuitive graphic overlay. Clear labeling, good contrast, and comfortable key spacing make a panel user-friendly.
Embossed keys enhance usability. Raised areas guide the finger, making it easier to find buttons without looking. Combined with backlighting or indicator LEDs, they create a confident, fast interaction.
Tactile response is often what users remember. The right dome gives satisfying feedback. Most tactile domes work best at 180–280 grams actuation force.
Long-life materials and domes rated for 1 million cycles or more ensure the panel stays reliable. In harsh environments, overlays need UV resistance, and circuits should be sealed against moisture.
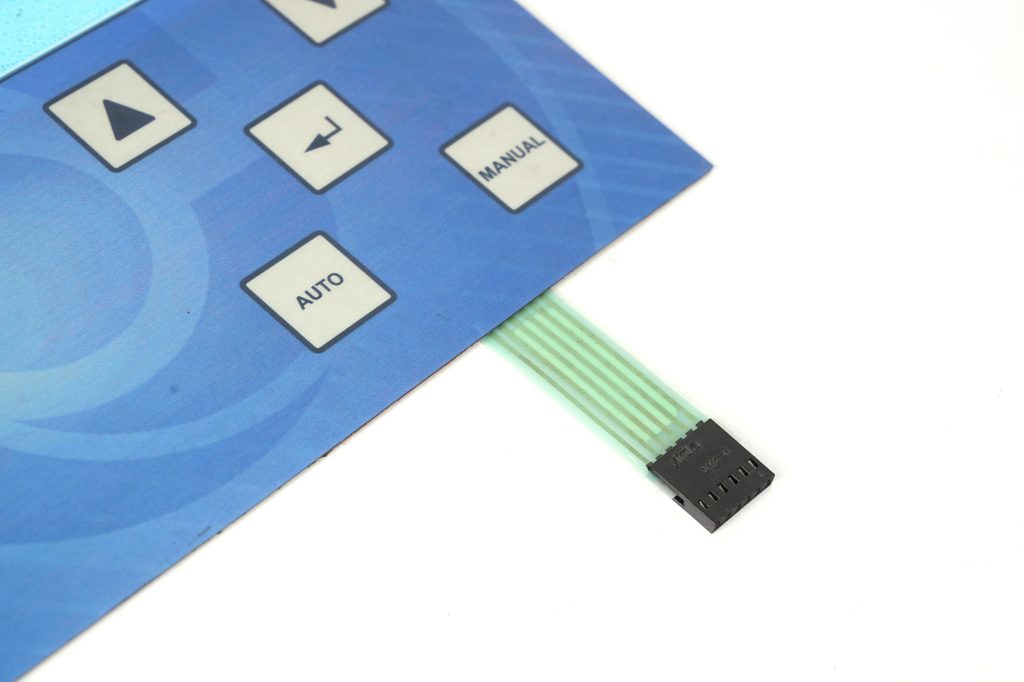
Adhesive strength matters too. A panel should stay firmly attached without bubbling or peeling. Use adhesives rated for temperature extremes or exposure to cleaning agents, if needed.
Tactile vs. non-tactile: which is better?
Tactile membrane switches are ideal for environments where physical feedback helps. Pressing the button gives a mechanical click. This is useful in gloves, on machinery, or for older users who benefit from feel-based confirmation.
Non-tactile switches, on the other hand, offer a sleek, quiet interface. They also tend to last longer because there’s no dome to wear out.
Some products even combine both. Use tactile feedback for key functions, and non-tactile in secondary areas. For industrial, medical, or field tools, tactile is often the better option. For minimal or modern consumer designs, non-tactile may be the right choice.
Can membrane switches handle harsh environments?
Yes. With the right design, membrane switches can thrive in tough settings.
Use sealed designs with edge gaskets or perimeter adhesives. This blocks dust, dirt, and water. For extreme environments, IP65 or IP67-rated sealing is available.
Choose UV-resistant overlays for outdoor use. Sunlight fades graphics and weakens plastics, but UV-stable PET holds up well. For extreme temperatures, select heat-stabilized materials rated from -40°C to 85°C or higher.
Add chemical resistance where needed. Industrial or medical environments often involve alcohol wipes, oils, or solvents.
Some switches include EMI/RFI shielding for electronics in sensitive environments. This keeps interference low and improves safety.
What testing is needed for membrane switch panels?
Actuation life testing checks how long buttons last. Quality tactile domes should reach 1–5 million presses. Non-tactile switches usually last even longer.
Electrical testing confirms signal consistency and circuit integrity. It checks for shorts, opens, and resistance. Every button should activate precisely, without false signals.
Environmental testing includes heat, cold, humidity, and UV exposure. Switches are placed in chambers simulating harsh conditions to verify performance. This step is vital for outdoor or industrial use.
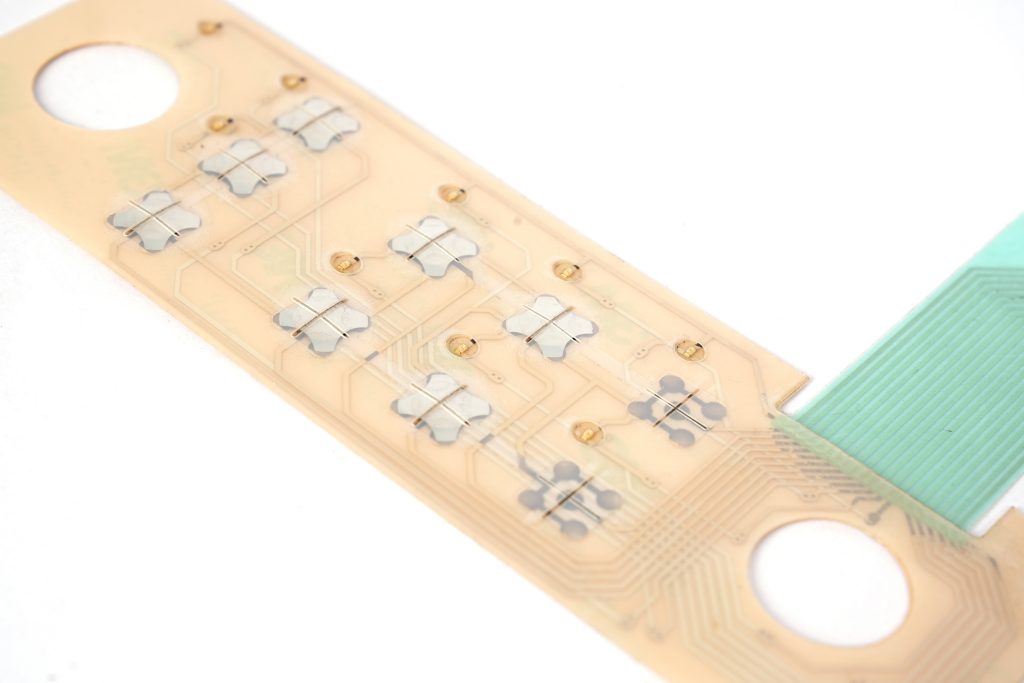
Adhesive strength testing makes sure panels won’t peel or shift. Poor bonding can lead to safety issues or malfunction.
Conclusion:
Membrane switches are the heartbeat of many control panels. Their success lies in smart design, careful material selection, and clear focus on user needs. With multiple types to choose from—tactile, non-tactile, backlit, capacitive.
For expert support with your membrane switch design, reach out to sales@best-membraneswitch.com
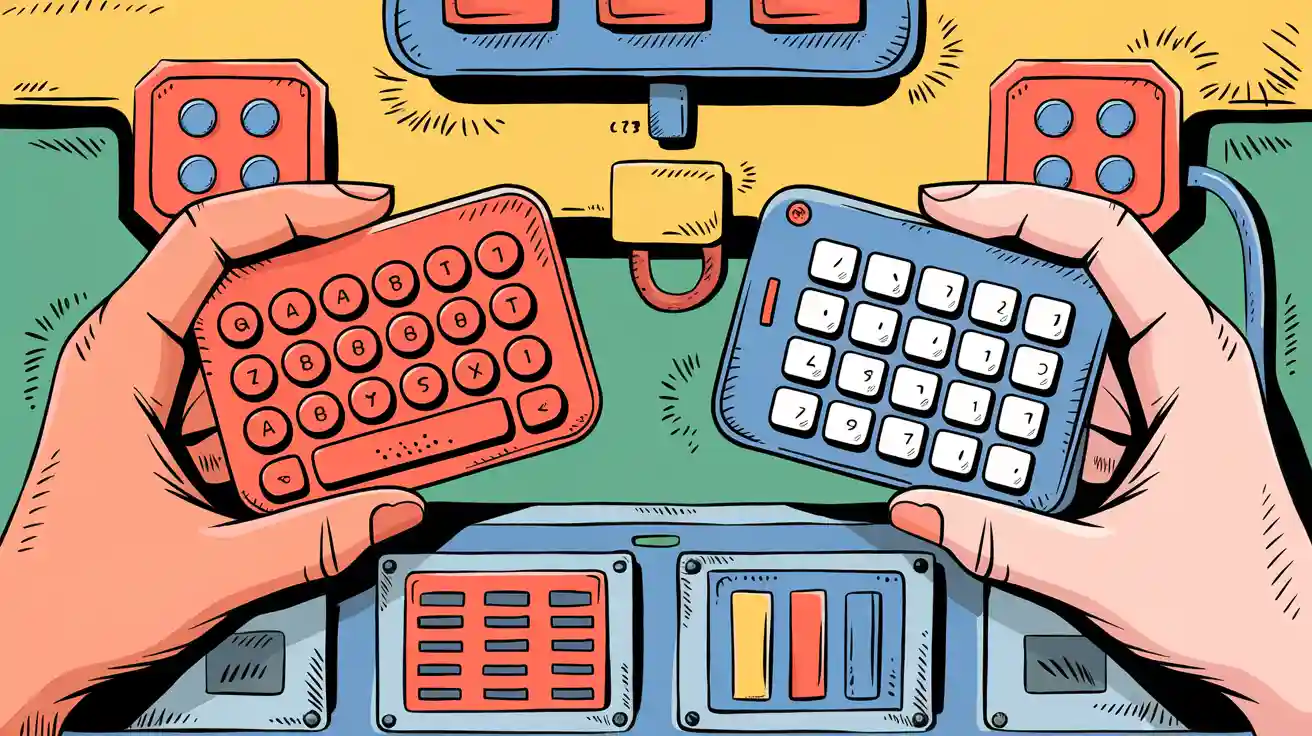
Rubber Keypads and Plastic Keypads Which Performs Best in Industry
Rubber keypad stands out as the top performer in industrial environments. Industrial buyers value this option for several reasons: These factors directly impact efficiency and reliability in factories, workshops, and production lines. Key Takeaways Performance Overview Key Factors Industrial environments demand keypads that deliver consistent performance and withstand harsh conditions. Manufacturers evaluate keypads using several ...
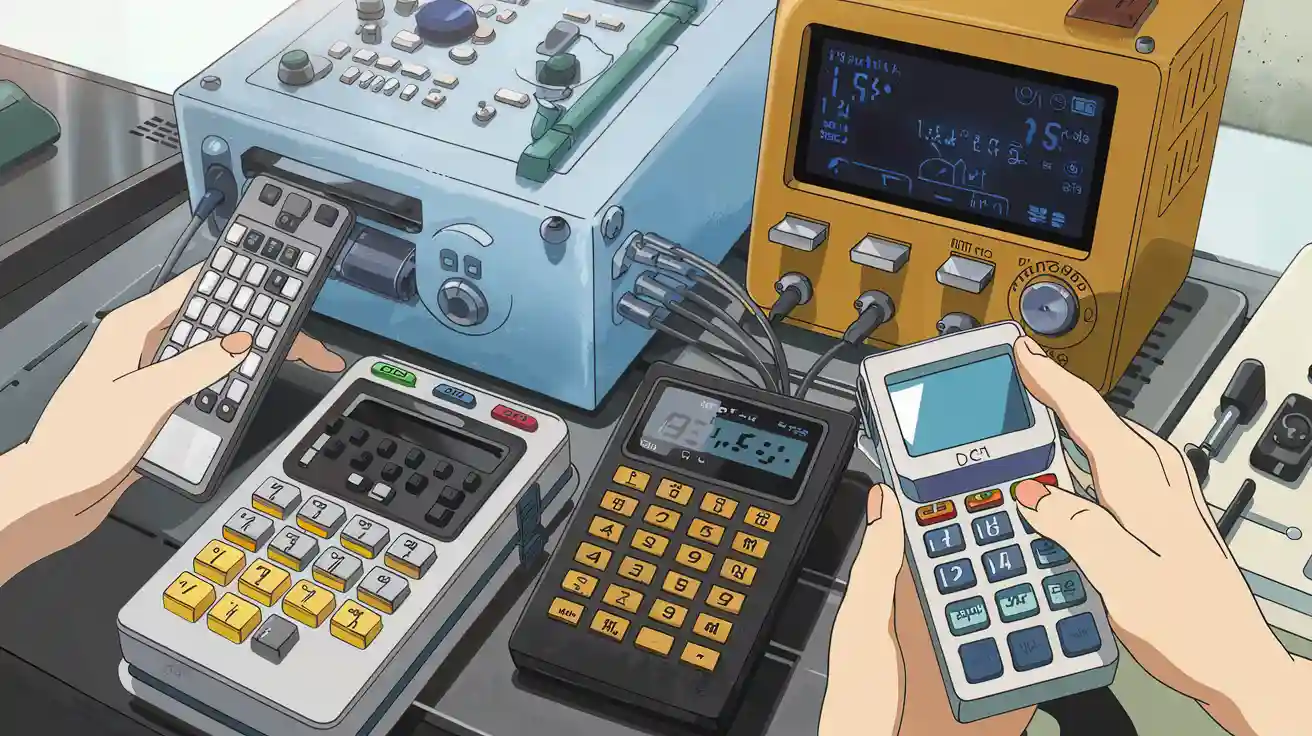
Top 10 Applications for Silicone Rubber Keypads in Modern Electronics
Silicone rubber keypads play a vital role in modern electronics, offering exceptional longevity and reliability across a wide range of applications. Key Takeaways Consumer Electronics Silicone rubber keypads have become essential in consumer electronics, supporting a wide range of applications from mobile phones to gaming devices and music players. Manufacturers choose these keypads for their ...
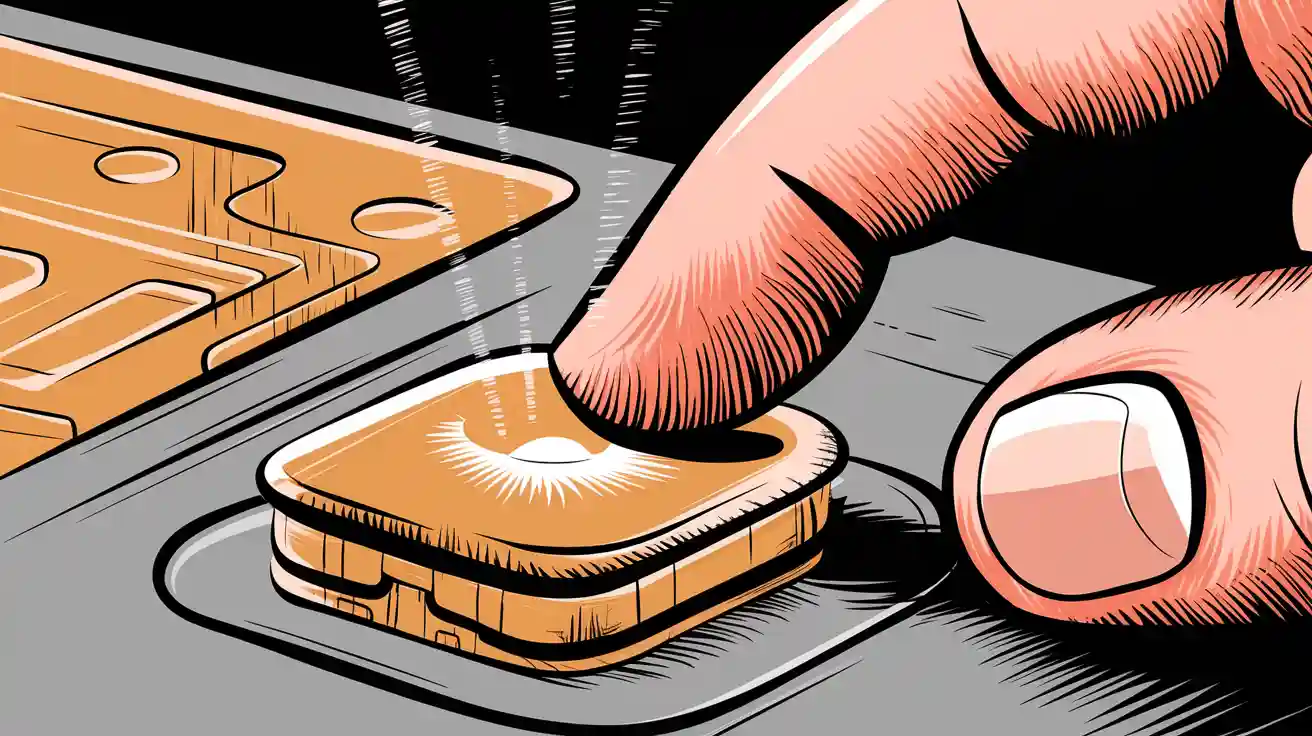
Why Input Solution Key Membrane Protection Matters in Modern Devices
When my device stopped working during a critical project, I quickly realized the input solution key membrane had failed. I learned that protecting this membrane is essential for any keyboard or device. The input solution key membrane shields sensitive components from dust, moisture, and heat. Without proper membrane protection, I have seen keyboards malfunction, leading ...
Contact us online